News
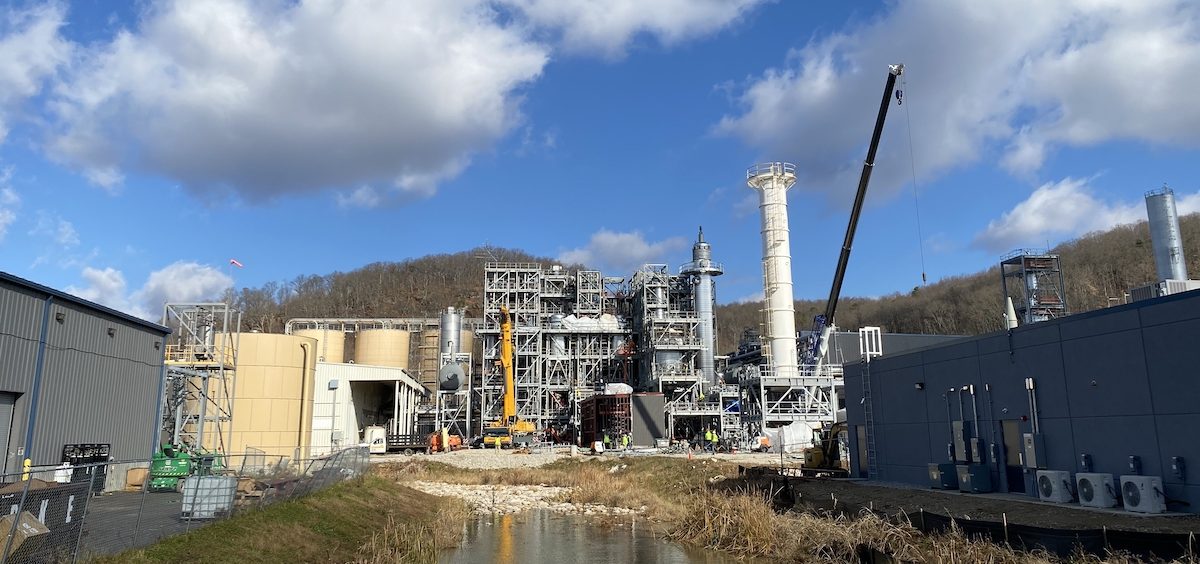
A new plant in Ironton uses cutting-edge technology to recycle plastic waste
By: Taylor Burnette
Posted on:
IRONTON, Ohio (WOUB) — “A molecular washing machine” is how PureCycle’s CEO Dustino Olson describes the company’s plastic recycling process.
At their recently constructed plant in Ironton, all sorts of plastic comes in: bottles, packaging, containers and more. And at the end of the process is a clear plastic pellet, a product that Olson said adds value to what often would just be going into the landfill.
“It’s difficult to find anybody in the world that doesn’t want recycled product,” Olson said. “But the quality of the product hasn’t been good enough to go everywhere.”
While the manufacturing facilities at the plant are still under construction, it is expected to be fully operational in early 2024. Olson said the facility can produce 107 million pounds of recycled polypropylene product, each of which brings in 75 cents to $1.50 per pound. This goes back into the local economy and beyond. In addition to the economic boost, the plant also brought around 100 new jobs to Ironton, Olson said.
“We’re creating a product that’s unique. We’re creating a technology that’s never been done before,” Olsen said. “It gives other locations … incentive to go get that plastic waste and bring it to us, because we can create value out of it. There hasn’t been that value motive to do this business until we came around. So there will be waste that comes in from other areas of the country.”
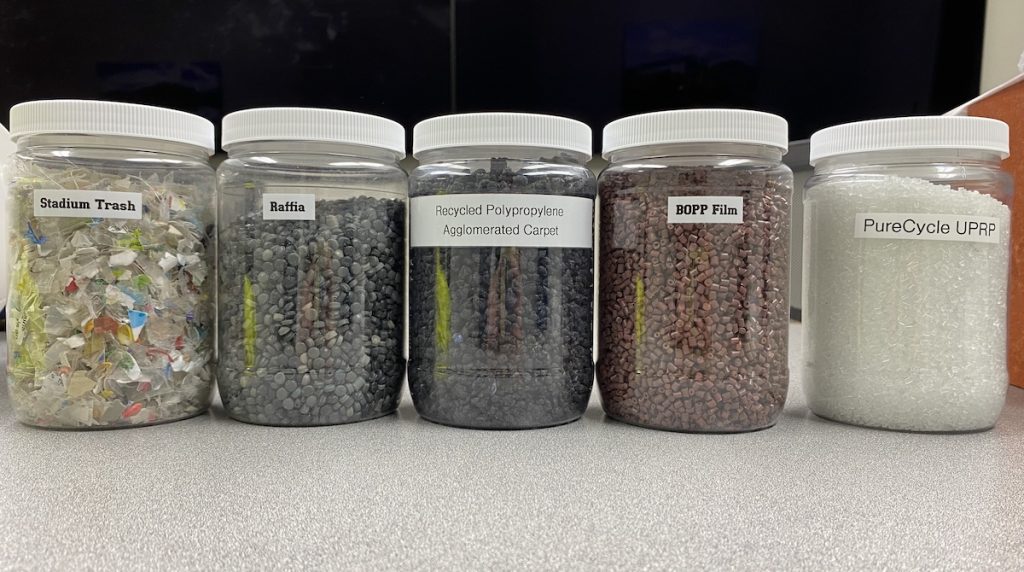
At the Ironton facility, PureCycle has facilities for washing and preparing plastic as well as for the actual refining process. It also has a smaller scale of the plant used to test its process.
In the smaller facility, Olson sticks his hands into a barrel and pulls out a cupped handful of feedstock — little rounded clear pellets that are the final product of the “molecular washing machine” recycling process. It smells like most other virgin plastics, and it can be used like them too.
Walking through the preparation facility, where PureCycle takes bales of plastic waste, breaks them down, grinds them and cleans them, it is hard to picture how such a broad array of plastics can become feedstock. Bottles, containers, and an array of other disposable plastic items are all collected in the facility to become reusable.
After the plastic waste runs through the preparation facility, it goes to the purification plant. Micheal Weber, the vice president of technology at PureCycle, said that plastic recycling can be as simple as melting plastic down into new shapes, or as complex as breaking the plastic down to its fundamental building blocks.
“We’re somewhere in the middle,” Weber said. “We’re doing a minimal amount of energy, just removing contaminants that can restore the plastic back to its original state.”
James Eagan, associate professor at the University of Akron’s School of Polymer Science and Polymer Engineering, researches the effective use of plastics. The proper appearance, scent and feeling of recycled plastic is important to its viability economically, Eagan said.
“Recycling is dirty business,” Eagan said. “Being able to clean it up with an innovative process really is essential to increasing the amount of material that we recycle yearly.”
PureCycle is also located in a favorable location for this type of recycling because Ohio is one of the largest consumers of polypropylene resins and producers of polypropylene plastics.
“The transportation costs and the emissions associated with transporting polypropylene to such a facility, and then back to a resin producer or a consumer of recycled polypropylene is very favorable for our region,” Eagan said. “I think it’s likely that the economics and the environment benefits will work out in their favor because of the location of their facility.”
Olson also mentioned that despite running on coal-based electricity, the company’s carbon footprint is 35% less than producing new polypropylene, and it uses 80% less energy.
“You’ve got a product that used to go to landfill, or get burned, or leaked to the environment that now we’re recovering, and we’re doing something with it,” Olson said. “It’s a product that’s a higher quality than the existing operations out there.”
PureCycle plans to open a second facility in Augusta, Georgia, in 2024, and Weber said it hopes to expand production to plastics other than polypropylene.